The First Characteristic of the Warehouse of Horrors: Disorganisation
One of the most terrifying aspects of any monster is its chaotic and disjointed appearance. Think of Frankenstein’s monster, assembled from mismatched parts, creating a jarring, unsettling sight. Similarly, a disorganized warehouse presents a chaotic environment where nothing seems to fit together properly.
Picture this: you step into your warehouse, and it’s a scene of utter disarray. Boxes from different shipments are piled haphazardly, making it nearly impossible to find essential items for picking and packing. The clutter isn’t just an eyesore—it’s a breeding ground for accidents and costly mistakes. According to a 2024 study by the Warehouse Education and Research Council, disorganized warehouses experience a 45% increase in operational errors, directly impacting both safety and profits. The stakes are high, and a disorganized warehouse is a ticking time bomb.
If you are in the fulfillment sector, you already know how disorganization can adversely impact your progress. It’s not just about money, either; a disorganized warehouse space will also negatively affect the morale of your team, which is an even greater loss since it will lead to a decrease in productivity as well. A disorganized warehouse layout also means that you and your team are more prone to safety hazards, which can put you at serious risk.
So, of course, disorganization is a very distinct part of the Warehouse of Horrors.
Second Characteristic: Seasonal Chaos
Festivals like Christmas, Diwali, and Thanksgiving are generally a cause for joy. For the general public, yes, but particularly for business owners. This is because the times when these events come around, depending on where you are, call for the peak season of sales. No matter what the nature of your business is, you are likely to experience a surge in your sales during peak season, which means growth for your business and even more profits. It’s truly a time for celebration!
But beware; the Warehouse of Horrors can dampen even the most festive spirits. One of its major pitfalls is poor preparedness for seasonal demand surges.
Some of your products will gain traction during certain times of the year. For example, if you sell fancy clothing, you will experience a surge in your sales around Christmas/New Year times.
If you are not prepared to deal with this surge, your warehouse can very well turn into the most chaotic place you will ever set foot in. And by prepared, we mean prepared from every possible angle. It would include not only making sure that you have enough inventory but also ensuring that your workforce and workflows are fit enough to deal with the fluctuations that come with this season.
If not? Well then, congrats, you have yourself the Warehouse of Horrors.
Third Characteristic: Lazy Order Management
Laziness is never a good thing; which is why it belongs to the Warehouse of Horrors. When laziness is paired with order management, you get truly disastrous results, which can throw your fulfillment efforts simply down the drain.
Your order management system is a critical point of interaction between you and your customers. This is because your customers will judge you based on how well you process their orders. And as easy as it sounds to ensure this, it really isn’t.
Even the smallest of mistakes in the order management system can cost you the trust of your customers. What if you don’t process the refunds on time? What if you make inaccurate deliveries? What if your team fails to respond to the Warehouse of Horrors in time?
If any of that happens, you’re already in the Warehouse of Horrors—and once you’re in it, it’s hard to get out (cue real spooky music).
Fourth Characteristic: Poor Damage Control
Damage is a part of life, and by extension, a common occurrence in every warehouse ever. However, in the ever-special Warehouse of Horrors, damage is an all-pervasive, always-present part of the processes, which is, of course, problematic.
Because, see, although damage will always be a part of your warehousing journey, you can take steps to reduce it and to optimize your processes in a way that doesn’t take a drastic toll on your services. Mostly, this will involve installing equipment like protective gear, lockout systems, anti-slip tape, low-clearance warning bars, and conveyor systems. This is what will help you keep your team and your inventory safe.
Needless to say, the Warehouse of Horrors does not entertain any of this and is hence a pretty dangerous place—both for you and for the development of your business.
Part 2: The Escape Plan
There is light at the end of even the darkest tunnels, and hence, even the notorious Warehouse of Horrors comes with an escape plan.
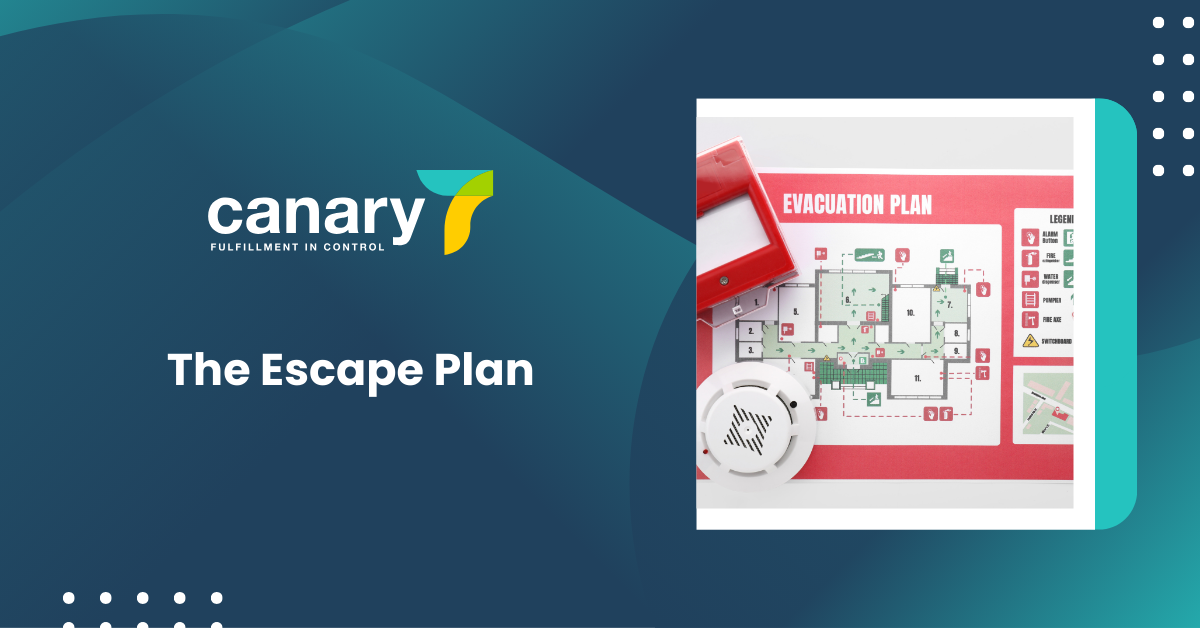
In simpler words, if you want to avoid the possibility of your warehouse ever turning into the Warehouse of Horrors, you can. And the best part is there is only one thing you need if you want to do that.
Automation.
Yes, you heard us correctly: by automating your warehouse processes, you can ensure that your warehouse remains in optimal condition, effectively avoiding the fulfillment nightmare.
Step 1: Assess Your Current Processes
Start by evaluating your existing workflows. Identify bottlenecks, repetitive tasks, and areas prone to human error. This assessment will serve as the foundation for your automation strategy.
Step 2: Implement Warehouse Management Software (WMS)
A robust Warehouse Management System (WMS) like Canary7 can revolutionize your operations. By 2024, warehouses using WMS saw a 30% reduction in picking errors and a 25% increase in efficiency. The system optimizes your layout, ensuring that every square foot is used efficiently, and streamlines order processing, so you’re always prepared—even during peak seasons.
Step 3: Integrate Automation Tools
Beyond WMS, consider integrating automated picking systems, conveyor belts, and real-time inventory tracking. These tools not only reduce labor costs but also minimize errors, leading to faster fulfillment times. A recent report by MHI found that warehouses implementing these technologies experienced a 40% improvement in overall productivity in 2024.
The Benefits of Automation
Automation offers a myriad of benefits, including:
- Enhanced Organization: Automation streamlines your warehouse layout, ensuring a systematic, efficient arrangement that boosts productivity.
- Peak Season Preparedness: With precise forecasting and efficient stock management, automation ensures you are well-prepared for seasonal demand surges.
- Improved Order Management: Automation enhances your order processing accuracy and speed, leading to better customer satisfaction.
- Prompt Damage Control: Automated systems reduce the risk of damage and ensure swift, effective responses to any issues, safeguarding both your inventory and workforce.